How the Right ERP Configuration Delivers Traceability in Manufacturing
This blog originally appeared on the FABTECHEXPO.COM site, released on August 12, 2019.
Jeffrey Sawka, ERP/MRP Software Consultant / Implementer and FABTECH 2019 Speaker
I’ll be talking about material handling, traceability and ERP configuration at FABTECH in November. Here’s a slice of my presentation.
Manufacturers and processors continue to face challenges with traceability. They need to trace parts at the material, work center and operator level while also minimizing production container and hi lo movement. If a quality problem occurs, enterprises must have the means of tracing back through the manufacturing process to the origin of the raw material.
An Analogy
I like the analogy of making baked goods. If I’m making cakes (which I love, by the way, chocolate especially) and each cake requires one stick of butter, traceability is easy as…(should I say it)…pie! But what if my cake requires 2/3 of a stick of butter? My first cake gets 2/3 of a stick of butter from the first stick, leaving 1/3 stick left over. My second cake will use the 1/3 stick from the first stick and then another 1/3 stick from the second stick of butter.
When I sell my cakes by the slice, how do I trace where the butter came from?
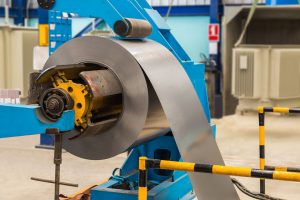
Cold rolled steel coil on decoiler of machine in metalwork manufacturing
Or take parts made from coils of steel when a manufacturer is doing a combined lot of raw materials going into a manufactured lot. For example, we might have a bin of 300 steel parts, and 200 come out of one coil of steel, and we still need 100 parts from another coil of steel to add to that bin to move it forward. The traceability gets even harder when I manufacture in sizes of 300 but pack and ship in containers of 50.
How do I assign traceability of the 50s to that manufactured bin of 300?
That’s where properly configured ERP software comes in.
It’s All About the ERP Configuration
Many manufacturers find it difficult to make the type of transaction I just described and record it properly – traceability sometimes goes out the window. When every third lot comes from a mixed lot of raw materials and systems aren’t configured to recognize them as such, traceability fails.
The best practice for traceability is to configure ERP software to capture the transaction and to do so as simply as possible so that the operator isn’t even aware that it’s happening. That’s when you’ll get the traceability you want – capturing the transaction within a difficult environment while making it easy on the operator.
Some ERP solutions can do this if they are properly configured. It’s more than a matter of a function or module – it’s about how the system is configured to achieve 100% traceability.
Limiting Container Size Changes/Hi Lo Movements
Another way to achieve improved traceability is to limit container size changes and avoid extra hi lo movements of containers. It’s challenging space-wise and cost-wise to make sure I have the same sized container throughout my production process. It means extra material handling, more space requirements, and significant costs.
Think about lot control from a different perspective, that is, to configure lot control to minimize container movement to gain perfect traceability.
When the ERP software is properly configured, it meets the end goal of traceability rather than disrupting the shop floor process.
This is a just a slice of the presentation I’ll be giving at FABTECH on material handling, traceability and ERP configuration.
Hear more from Jeffrey during FABTECH session “How to Keep Full Traceability of Parts (Material, Workcenter and Operator) While Minimizing Hi Lo Moves (Container Movement)”.